Crane Hi 4 Repair Manual
ISSUES: Harley Davidson recommends both gear lube and motorcycle oils for their equipment and there are many different models with corresponding specific oil recommendations. The variety of recommendations can cause confusion and lack of confidence in making the correct AMSOIL lubricant recommendation. The following charts outline the proper sequence of product recommendations for the Harley Davidson products listed. DESCRIPTION & RECOMMENDATIONS: Harley Davidson manufactured 9 types of engines from 1929 to the current model year. Flathead (1929-1974), Knucklehead (1936-1947), Pan- head (1948-1965), Shovelhead (1966-1984), Evolution (Blockhead) 1340 (1984-1999), Twin Cam (2000 to current), V-Rod (Revolution) (2001 to current) Ironhead Sportsters (1957-1984) & Evolution Sport- sters 1985 to current.
Harley Davidson recommends SAE 60 or SAE 50 engine oil for Flathead, Knucklehead, Panhead, and Shovelhead equipped bikes. AM- SOIL recommends AHR SAE 60 or MCV 20W-50 motorcycle engine oil for these vintage models. AMSOIL SVT or SVO should be used in transmissions found on these models. Shovelhead is the only model with a chain case that is lubricated via engine oil. AMSOIL recommends MCV 20W-50 motorcycle oil in all 3 holes (engine, transmission, and primary chain case) on Evolution 1340 and all Twin Cam engines.
AMSOIL recommends SVT as a secondary oil for the transmission, and SVO as an option for older transmissions. New seals are recommended where excessive leaking is evident. Ironhead, Evolution Sportsters and V-Rod use one lubricant for both the engine and transmission and AMSOIL recommends MCV motorcycle oil for this common sump.
Harley Davidson has manufactured 9 types of engines from 1929 to the current model. Flathead (1929-1974), Knucklehead (1936-1947), Panhead (1948-1965), Shovelhead (1966-1984), Evolution (Blockhead) 1340 (1984-1999), Big Twins 1450 (2000 to current), Revolution/V-Rod (2001 to current) Ironhead Sport- sters (1957-1984) & Evolution Sportsters 1985 to current. Harley Davidson recommends SAE 50 or 60 for the engine oil in their Flathead, Knucklehead, Panhead, and Shovelhead. AMSOIL recommends AHR SAE 60 or MCV 20W-50 motorcycle oil for all these older models.
Use AMSOIL SVG or SVO for the transmissions. Of these models only the Shovelhead has a chain case that is lubed, and is fed by the engine oil.
In the Evolution 1340, Big Twins 1450, and V-Rods, AM- SOIL recommends MCV 20W-50 motorcycle oil in all 3 holes (engine, transmission, and primary chain case). AMSOIL recommends SVG as an alternative oil for the transmission, and SVO as an option for older transmissions. New seals are recommended where excessive leaking exists. Harley Davidson has manufactured 9 types of engines from 1929 to the current model.
Crane Hi 4 Wiring
Flathead (1929-1974), Knucklehead (1936-1947), Panhead (1948-1965), Shovelhead (1966-1984), Evolution (Blockhead) 1340 (1984-1999), Big Twins 1450 (2000 to current), Revolution/V-Rod (2001 to current) Ironhead Sport- sters (1957-1984) & Evolution Sportsters 1985 to current. Harley Davidson recommends SAE 50 or 60 for the engine oil in their Flathead, Knucklehead, Panhead, and Shovelhead.
AMSOIL recommends AHR SAE 60 or AMV 20W-50 motorcycle oil for all these older models. Use AMSOIL SVG or SVO for the transmissions. Of these models only the Shovelhead has a chain case that is lubed, and is fed by the engine oil. In the Evolution 1340, Big Twins 1450, and V-Rods, AM- SOIL recommends AMV 20W-50 motorcycle oil in all 3 holes (engine, transmission, and primary chain case). AMSOIL recommends SVG as an alternative oil for the transmission, and SVO as an option for older transmissions. New seals are recommended where excessive leaking exists. Ironhead & Evolution Sportsters use one sump for both transmission and chain case.
AMSOIL recommends AMV motorcycle oil for this common sump. Disconnect the battery. Secure the motorcycle on a suitable stand with the rear wheel off the ground.
Remove components necessary for easy access to rocker covers, pushrod covers, and gear case cover, i.e., exhaust system, gas tank, air cleaner, foot rest, etc. Remove spark plugs. Remove top and middle sections of rocker boxes, then rotate engine so both valves are closed on the cylinder head being worked on (put transmission in high gear and move rear wheel to slowly rotate engine). Remove the two 5/16″ bolts nearest the rocker arm shafts (keep all shafts, rocker arms, and pushrods in order so they can be installed in their original position).
Remove the pushrod covers and pushrods. NOTE: The use of adjustable time-saver pushrods will simplify installation. Follow the manufacturer’s recommendations for installation of those parts. It is not necessary to remove the tappet guides if you use a cam installation tool such as Crane #9-0020 to hold the tappets in place during cam installation. If you remove the tappet guides, you must use a tappet block alignment tool such as Crane #9- 0021 to re-install the tappet guides. Tappets can be held up in place during removal of guides by using U-shaped piece of safety wire or paper clip hooked to the tappets.
Remove ignition covers on gearcase cover by drilling out rivets to gain access to sensor plate. Remove the inner cover, sensor plate and rotor. NOTE: For re-installation, use new rivets H-D #8699 or drill and tap for 10-32 screws. Remove the gearcase cover screws and remove cover while holding end of cam inward.
Now remove the camshaft, spacing washer and thrust plate. INSTALLATION Prepare the Motorcycle 1. Follow the Service Manual instructions to remove the seat.
To prevent accidental vehicle start-up, which could cause death or serious injury, disconnect negative (-) battery cable before proceeding. Disconnect the negative (-) battery cable from the battery. Place motorcycle on a lift and secure the front wheel. Use an overhead crane or hoist attached to the frame to lift the rear of the motorcycle to allow the rear fork to pivot through its range of travel. Place a screw jack under the rear wheel to support and adjust the rear fork during shock removal, installation and ride height adjustment.
Be sure rear wheel is supported when removing rear shocks. If wheel is not supported rear fork can drop down, which could result in death or serious injury. (00481b) Removal 1. See Figure 1. Remove the bolt and washer (1) that fasten each of the shock absorbers (2) to the rear fork. NOTE Snap-on Tool Co. Adapter, Part Number SRES 24, is necessary to gain access to the shock absorber bolts.
Remove the flanged locknut (6) and cup washer with grommet (5) fastening the shock absorber to the frame bracket (4) and remove the shock absorber. Remove, inspect and, if necessary, replace the rubber grommets, the cup washers (5), and the bushing (3). Repeat for the other shock absorber. Disassemble the Shock 1. Thoroughly clean the rear fork end of the shock, especially near the shock canister seal. Support the rear fork end of the shock absorber and shock canister on the table of a press.
Press on the shaft to compress the spring in the canister until the keeper plate drops down away from the retaining ring. Incoming search terms:. THROTTLE CABLE ADJUSTMENT A) Rotate the throttle grip to the full open position, look into the throttle bore and see if the throttle valve (slide) opens completely. If the throttle valve does not open completely unscrew the adjuster on the opening cable until it does.
This adjustment should be made carefully to assure maximum carburetor performance. After adjustment tighten the adjuster jam nut. B) After adjusting the open cable, adjust throttle freeplay with the closing (idle) cable to approximately 1/8″ an indicated in the following illustration. Note It is very important to adjust the cables in the preceding described manner to ensure that the idle cable operates correctly for safety.
It must close the throttle completely 2 PLEASE NOTE USE CAUTION PLEASE NOTE SAFETY WARNING pull open cable pull close cable SHOVELHEAD/IRONHEAD XL Installation Instructions Check and make sure that the throttle cables are routed properly by rechecking the throttle play as the handlebars are turned from side-to-side; the amount play should remain consistent. C) After the throttle cables have been adjusted, make sure that all the lock nuts are securely tightened. AIR CLEANER A) The air filter bracket is attached to the crankcase with 1 long bolt, and a bracket-spacer. Removed the crankcase nut located between the tappet blocks & replace it with the enclosed bracket spacer; tighten the spacer securely. B) Remove the stud protectors from the K&N filter and place the two backing plates on the studs. Now slip the the filter onto the carburetor.
C) Attach the 2 long brackets to the air filter studs with the enclosed nuts & flat washers, and to the bracket spacer with the enclosed bolt using the lock washers, and flat washers. When the carburetor and air cleaner are properly aligned, securely tighten all of the mounting hardware including the intake manifold clamps. In some cases it may be necessary to bend the brackets slightly to arrive at the correct fit. D) Use the enclosed hose clamps to secure the fuel hose to the petcock, and the HSR carburetor. The screw clamp goes on the petcock end and the spring clamp attaches to the carburetor end. E) Attach the chrome air filter cover with the enclosed socket head screw. CHOKE CABLE INSTALLATION A) Attach the Mikuni choke cable bracket to the original choke cable bracket on the air cleaner stud with the enclose hardware as illustrated.
PICKUP PLATE INSTALLATION Remove the existing trigger/points plate and rotor, points cam and advance. Refer to the bike’s Service Manual for the proper procedure. EVOLUTION AND LATE MODEL SHOVELHEAD V-TWINS 1. From inside the cam/ignition housing, feed the free end of the MSD pickup harness through the wire access port. Note: The harness includes a heat-resistant acrylic sleeve that fits snugly inside the port opening. Do not pull the sleeve completely through the port.
It must be positioned to protect the wires as they pass through the port opening. Mount the MSD pickup plate inside the housing (Figure 1).
Note the “adjusting notch” on the edge of the plate. This notch must be located over the series of “steps” inside the housing (about the 7 o’clock position as you face the housing). One of the sensor units will be at approximately 12 o’clock. SPORTSTER MODELS 1. On Sportsters, the wire access port must be enlarged. Use a 9/32″ drill bit to enlarge the wire port. Remove the wire harness clamp of the pickup assembly and route the wires through the port.
Mount the MSD pickup plate inside the housing (Figure 2). Note the “adjusting notch on the edge of the plate.
This notch must be located over the “cast notch” inside the housing (about the 11 o’clock position as you face the housing). The shorter of the two sensors will be approximately in the 9 o’clock position.
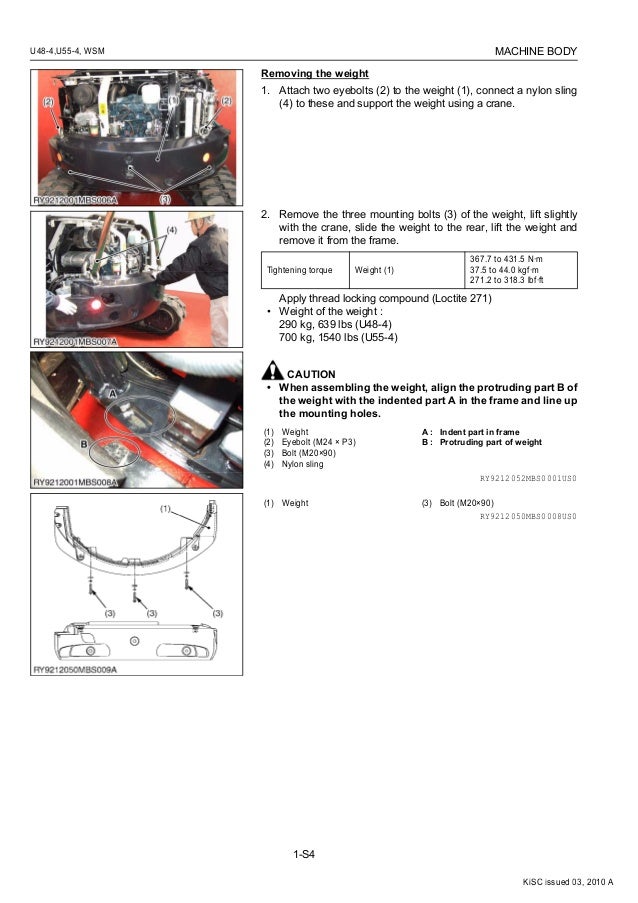
Install the hold-down/standoff screws with flat washers until they are snug – do not tighten at this time (Figure 3). Put the MSD rotor in place on the end of the camshaft. The locating pin in the rotor bore must align with the groove in the cam. Do not force the rotor on the camshaft!
Push the rotor into place until it is tightly against the end of the cam then snug the retaining screw. Check the distance from the outer surface of the pickup plate to the end of the installed rotor (Figure 4). If necessary, add shims until the measured rotor height is 9/16″ (+/- 1/32″). When the rotor height has been verified, remove the retaining screw, place a drop of Red Loctite on the threads and reinstall the screw to the factory recommended torque Incoming search terms:.
Citroen berlingo recenze. Ebook Citroen Berlingo Zooom Workshop Manual currently available at www.karenniwomen.org for review only, if you need complete ebook Citroen Berlingo. Citroen berlingo & peugeot partner owners workshop manual john s mead models. For citroen berlingo zooom workshop manual is available in various format.
. On this page, you are viewing a list of part ads for sale, divided into a number of pages. Type: Manuals. Every product from the list has images and descriptions, and a list of specifications.
Above the table, please click a column label to sort the part listings, another click of the same label will sort the listings in reverse order. You may also sort the part listings by selecting an option from the Sort selection boxes, also located above the table. From the drop-down list on the left side of the page, you can select and filter by type, manufacturer, brand, as well as by other product specifications. Clicking the Reset button will clear all criteria and bring you back to the Manual Sales listing.
Crane Hi 4 Repair Manual Pdf
The parts filters are set to ease you in the process of finding the desired results. Buy a Manual from an industry leader in Manuals for sale! New Manuals and Used Manuals for Sale and Rental. Manuals for sale at.

Search from 1000's of Manual listings for new and used Manuals updated daily from 100's of dealers. Buy high quality used Manuals from our network of worldwide locations for used Manuals and quality lift equipment.
Manual Sales - find Used and New Manuals for Sale and Rent amongst extensive inventory listings on CraneNetwork.com. Manuals for sale and rent. See all parts for sale on the, a leader in Manual Sales. Over 30,000 companies and individuals rely on our online services to effectively manage their fleet for the sale and rental of cranes and equipment.